Both high alumina bricks and fire clay bricks contain alumina, however, the overall performance of high alumina bricks is better than that of refractory clay bricks at high temperature. Why is that? In fact, high alumina bricks contain more Al2O3 than fire clay bricks.
For high alumina bricks and clay bricks, alumina is the main component. The performance of refractory bricks at high temperature varies with different alumina content. Bricks containing more than 55% alumina are high alumina bricks, while those containing less than 55% are refractory clay bricks.

Notes:
Fire clay bricks are cheaper than aluminum bricks. But that's not to say we don't consider fire clay bricks when we choose firebricks. Both high alumina bricks and fire clay bricks can be used to build kilns or furnaces. However, certain parts of the kiln or furnace operate at lower temperatures, and in these places, you can choose clay bricks to reduce costs without affecting the overall production performance of the kiln.
High alumina bricks have high density, low porosity, high mechanical strength and wear resistance. The refractoriness and load softening temperature of aluminum bricks are higher than those of fire clay bricks, and the slag corrosion resistance (especially to acid slag) is better, and these properties increase with the increase of Al2O3 content. Because of the densivity of high alumina brick is better than that of clay brick, high alumina brick has lower thermal stability than clay brick.
High alumina brick properties:
1.High temperature resistance
With the increase of Al2O3, the glass phase in firebrick decreases and the percentage of mullite and corundum increases, so the bulk density and refractoriness also increase.
2.Softening temperature under load
Because high Al2O3 in high aluminum products, less miscellaneous mass, the formation of less fusible glass, so the load softening temperature is higher than clay brick.
3.Reheat change
At 0 ~ 1000℃, clay brick expands with increasing temperature, and the expansion rate is between 0.6% ~ 0.7%. When the temperature rises above 1200℃, the volume of the clay brick will begin to shrink.
High alumina brick is mainly used for laying blast furnace, hot blast furnace, electric furnace top, rotary kiln lining, etc. In addition, high alumina brick is widely used as open furnace regenerative lattice brick, water brick and so on.
Due to the low softening temperature of fire clay bricks under load and shrinkage at high temperature, fire clay bricks can only be used in the secondary parts of the kiln, such as the wall of the regenerator chamber, the lining brick of the small flue and the lattice brick of the regenerator chamber, the lining brick of the furnace door, the lining brick of the furnace top and the lining brick of the rising pipe.
However, the price of high aluminum bricks are higher than that of fire clay bricks, so it is unnecessary to use high aluminum brick where clay brick can meet the requirements.
Notes:
High aluminum bricks are used to build the furnace head of the coke oven combustion chamber and the bottom brick of the carbonization chamber. However, it is not suitable for the wall of the carbonization room, because the high alumina brick is easy to produce the edge and warpage Angle at the high temperature of carbonization.
High alumina brick factory
Kerui has a professional construction team and advanced technology, our refractory products have been sold to Russia, Korea, Ukraine, Brazil, Indonesia, Iran, Thailand and other countries. Corey has been specializing in refractory performance research, to provide customers with professional services, we hope to become your best partner in China.
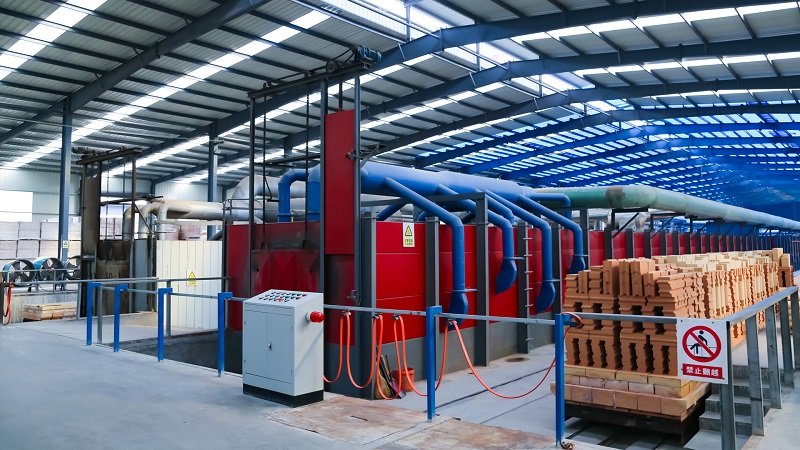
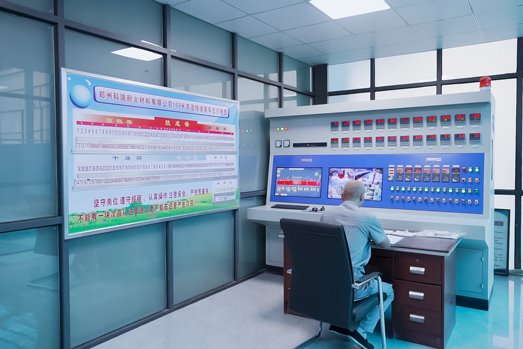
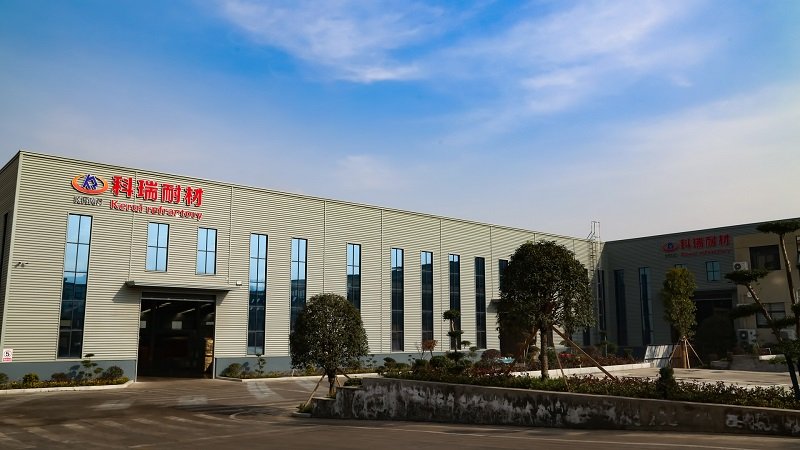